Hipot Testing for Traction Motor
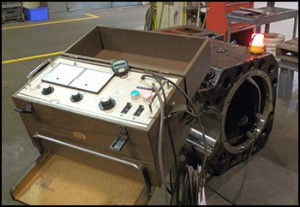
Hipot Testing of a traction motor
A high potential (hipot) test verifies that the insulation of an energized product or component is sufficient to protect the operator, system or connected components from electrical shock.
A typical electric wire has one or two components: a wire conductor along which the current flows, and insulation (aka dielectric) that shields the conductor from direct contact with other wires. Some wires also contain a third component, metallic shielding, between the conductor and the insulation. The question is: will the insulation do the job it was designed to do? If not, its failure could cause injury, loss of life, and damage to expensive equipment along with costly downtime.
A hipot test applies high voltage between a product's current-carrying conductors and its metallic shielding. The hipot tester measures current that flows through the insulation, known as dielectric leakage current. Hence, when a deliberate over-application of test voltage doesn't cause the insulation to break down (in other words if the insulation sufficiently withstands the voltage under normal operating conditions without allowing it to “leak out”), the product is considered safe under normal operating conditions.
The first technology to make use of insulation was electromagnetic telegraphy, the telegraph. Among the first to produce wire insulators for telegraph poles in the 1840s were Stiff and Doulton (UK). In 1865, Louis Cauvet patented a novel process to create ceramic insulators in the US. However, in the late 19th century, rising labor costs combined with the establishment of municipal electrical codes and the widespread development of high voltage and high amperage technologies required alternate technologies to augment or replace existing ceramic and tar-impregnated cloth insulation in use at that time. Hence, a need quickly emerged for accurate testers to detect an insulator's propensity for polarization, as well as faults such as opens, shorts, and miswiring. While a low potential test detect such faults, it can't detect shorts unless metal touches metal (aka dead short). However, there are many instances where flaws in or damage to the insulation or external factors cause shorts (near shorts); these include:
- Chemical (inorganic and organic compounds) or saltwater intrusion
- Contaminants (conductive dusts, moisture, dirt, volatile gases or compounds, solder and solder flux)
- Dirt
- Fatigue
- Humidity
- Material and workmanship defects
- Shock
- Stray wires
- Vibration
These can cause shorts between wires that are extremely close, but not touching (aka near shorts). In such cases, a dielectric withstanding voltage (hipot) test detects leakage that low potential tests miss. Starting in the 1930s, a number of US companies developed or assisted in the development of standardized hipot technologies and methodologies.
Since 1936, Associated Research has been providing test and measurement solutions for the electrical safety compliance industry. They were the first company to receive a UL listing and a CE mark for an electrical safety tester. In 1954, Elmer Slaughter delivered his dielectric tester to Westinghouse. In 1976, Slaughter Company delivered its first microprocessor-controlled automatic tester to McGraw-Edison. Today's high-speed automated testers using safety interlocks are controlled with the latest microprocessors running Apple, Linux and Windows platforms for the most sophisticated testing programs available.
<- - Make a Comment - ->