How Synchronous Motor Works?
Synchronous motor technology has its roots in the electricity and magnetism experiments of Michael Faraday in 1830 and his discovery that a changing magnetic field can induce an electric current. Two years later Parisian instrument maker, Hippolyte Pixii, built the first alternator consisting of a revolving horseshoe magnet passing over two wound wire coils generating a simple form of alternating current (AC). During the late 19th century, the advantages of AC over the existing direct current (DC) technology espoused by Thomas Edison, led many inventors in the United States and Europe, such as Nikola Tesla, to advocate the development of AC motors.
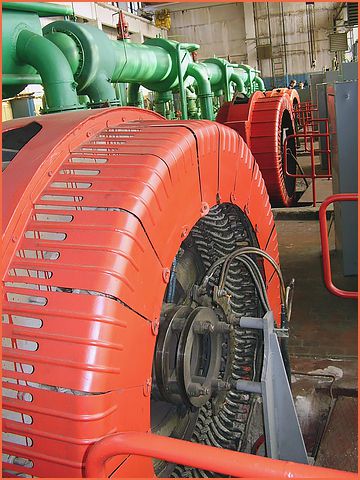
A century later, synchronous AC motors still represent one of most widely used technologies. Simply put, a synchronous motor is a rotary motor in which the speed of the rotating part or shaft is in synchrony or spins in tandem with the line frequency oscillations of the supply current (typically 60 Hz in the US and 50 Hz in Europe and Asia). To accomplish this, synchronous motors contain electromagnets usually on the rotor and a winding of a coil of copper wire (aka the field coil) around the stator ring. A small space, or air gap, separates the stator from the rotor, allowing the rotor to spin freely when the supply current is turned on. Depending on design requirements, the location of the electromagnets or field coil are interchangeably mountable on the stator or the rotor. When excited, electromagnets and the field coil work together to create a magnetic field that rotates in time with the oscillations of the line current. The rotor locks in, or turns in step, with this field at the same rate causing the shaft to rotate quickly. Once this occurs, the motor reaches steady-state operation and is in synchrony or “in sync”. If the motor load increases beyond breakdown load, the motor falls out of sync, and the field winding no longer follows the rotating magnetic field.
Synchronous motors are available in low and high horsepower industrial sizes. In low-voltage applications, synchronous motors are in use where precise constant speed is required. Small synchronous motors are able to start without assistance if the moment of inertia of the rotor and its mechanical load is sufficiently small. Small synchronous motors are commonly used in line-powered electric clocks and appliance timers.
Higher speed synchronous motors can drive hydroelectric turbines, injection process compressors, gas liquefaction machinery. However, above a certain size, synchronous motors are not self-starting. This is due to the inertia of the larger rotor; it cannot instantly follow the rotation of the magnetic field so it cannot accelerate to a synchronous speed without some supplemental mechanism such as a “pony motor,” which can accelerate a synchronous machine before the load is applied. In other applications, an amortisseur or “squirrel-cage” induction winding provides sufficient torque for acceleration and serve to dampen oscillations in motor speed. Once the rotor nears synchronous speed, the field winding is then excited, and the motor pulls into sync.
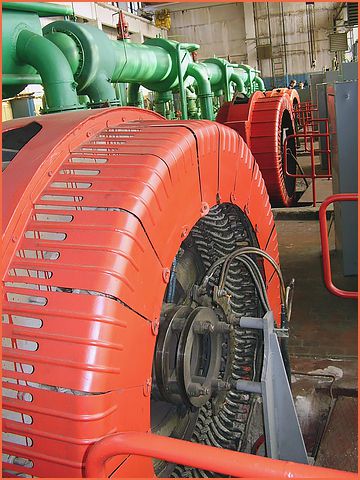
A century later, synchronous AC motors still represent one of most widely used technologies. Simply put, a synchronous motor is a rotary motor in which the speed of the rotating part or shaft is in synchrony or spins in tandem with the line frequency oscillations of the supply current (typically 60 Hz in the US and 50 Hz in Europe and Asia). To accomplish this, synchronous motors contain electromagnets usually on the rotor and a winding of a coil of copper wire (aka the field coil) around the stator ring. A small space, or air gap, separates the stator from the rotor, allowing the rotor to spin freely when the supply current is turned on. Depending on design requirements, the location of the electromagnets or field coil are interchangeably mountable on the stator or the rotor. When excited, electromagnets and the field coil work together to create a magnetic field that rotates in time with the oscillations of the line current. The rotor locks in, or turns in step, with this field at the same rate causing the shaft to rotate quickly. Once this occurs, the motor reaches steady-state operation and is in synchrony or “in sync”. If the motor load increases beyond breakdown load, the motor falls out of sync, and the field winding no longer follows the rotating magnetic field.
Synchronous motors are available in low and high horsepower industrial sizes. In low-voltage applications, synchronous motors are in use where precise constant speed is required. Small synchronous motors are able to start without assistance if the moment of inertia of the rotor and its mechanical load is sufficiently small. Small synchronous motors are commonly used in line-powered electric clocks and appliance timers.
Higher speed synchronous motors can drive hydroelectric turbines, injection process compressors, gas liquefaction machinery. However, above a certain size, synchronous motors are not self-starting. This is due to the inertia of the larger rotor; it cannot instantly follow the rotation of the magnetic field so it cannot accelerate to a synchronous speed without some supplemental mechanism such as a “pony motor,” which can accelerate a synchronous machine before the load is applied. In other applications, an amortisseur or “squirrel-cage” induction winding provides sufficient torque for acceleration and serve to dampen oscillations in motor speed. Once the rotor nears synchronous speed, the field winding is then excited, and the motor pulls into sync.
<- - Make a Comment - ->