Induction motor
You can divide the synchronous machines in 2 groups, based on the principle they employ to generate torque:
- interaction of 2 independent fields, one generated on stator and the other on the rotor: let's call this group "excited" synchronous machines;
- the torque is generated by an anisotropic rotor structure and the presence of a magnetic field generated by the stator: the latter field will tend to attract the anisotropic rotor in order to minimize the reluctance of the path of the magnetic field itself; let's call this group "reluctance" machines.
Then, of course, you can also mix the 2 things, by providing an anisotropic structure with some way (see down) to independently excite a rotor field.
Now, 2 additions to the above: in the 1st group the excitation of the rotor field can be provided by both a field winding fed with current through slip-rings and brushes (the traditional power plant alternator) and then will call it "electrically excited" synchronous; or, excitation can be provided by permanent magnets placed somewhere in the rotor structure (either on the outer surface or inside), and then we'll call it "PM synchronous" machine.
Second precaution: though the physical principle is the same, *synchronous* reluctance machines are quite different from *switched* reluctance ones. The latter, in fact, have a salient structure also on the stator, the coils being supplied (a phase at a time) with DC current, that produces a magnetic field fixed in space: once the minimal reluctance position is achieved, the rotor would continue stay there (neglecting little oscillations) unless current is moved to a different phase. In *synchronous* reluctance, instead, the stator structure is more conventional, almost isotropic, and a set of AC currents is supplied to all the coils: this generates a rotating magnetic field, hence your "preferred position" is not reached and the rotor continues spinning.
- interaction of 2 independent fields, one generated on stator and the other on the rotor: let's call this group "excited" synchronous machines;
- the torque is generated by an anisotropic rotor structure and the presence of a magnetic field generated by the stator: the latter field will tend to attract the anisotropic rotor in order to minimize the reluctance of the path of the magnetic field itself; let's call this group "reluctance" machines.
Then, of course, you can also mix the 2 things, by providing an anisotropic structure with some way (see down) to independently excite a rotor field.
Now, 2 additions to the above: in the 1st group the excitation of the rotor field can be provided by both a field winding fed with current through slip-rings and brushes (the traditional power plant alternator) and then will call it "electrically excited" synchronous; or, excitation can be provided by permanent magnets placed somewhere in the rotor structure (either on the outer surface or inside), and then we'll call it "PM synchronous" machine.
Second precaution: though the physical principle is the same, *synchronous* reluctance machines are quite different from *switched* reluctance ones. The latter, in fact, have a salient structure also on the stator, the coils being supplied (a phase at a time) with DC current, that produces a magnetic field fixed in space: once the minimal reluctance position is achieved, the rotor would continue stay there (neglecting little oscillations) unless current is moved to a different phase. In *synchronous* reluctance, instead, the stator structure is more conventional, almost isotropic, and a set of AC currents is supplied to all the coils: this generates a rotating magnetic field, hence your "preferred position" is not reached and the rotor continues spinning.
Theoretically, Yes, if the conditions under which it's running are constant (on squirrel cage induction motors). In reality, it varies due to a variety of factors. These can include changes in load, input power, environmental conditions, etc. Speed control really has 2 effects - providing a wider range of speed capabilities with the same motor (adjustability) as well as smoothing out (or at least attempting to smooth out) the effects that would change the motor speed and transients in loading, input voltage, etc.
Practically, NO, for electric motors connected to the AC power line. The speed of an AC induction motor is a function of the AC frequency, the number of poles in the motor, and the load on the motor. Under no-load conditions, the speed is quite constant. Under load, the speed will vary since the motor torque comes from the lag in the phase current. Unless the motor runs slower than synchronous speed, it cannot produce the torque necessary to do its work. Synchronous motors run at constant speed.
Practically, NO, for electric motors connected to the AC power line. The speed of an AC induction motor is a function of the AC frequency, the number of poles in the motor, and the load on the motor. Under no-load conditions, the speed is quite constant. Under load, the speed will vary since the motor torque comes from the lag in the phase current. Unless the motor runs slower than synchronous speed, it cannot produce the torque necessary to do its work. Synchronous motors run at constant speed.
Induction motors operate on the principal of current induction in the rotor which must rotate at a speed less than synchronous speed for induction to occur. This is referred to as slip speed and should not be confused with pole slipping.
Why induction motors have no pole slipping and why other motors have pole slipping. I will attempt to answer this but first let's define poles and synchronous speed in regards to electric motor operation.
Poles in an electric motor refer to the magnetic circuit poles and come in sets of two just like a common magnet. One is north (N) and one is south (S). If a motor has two poles, it will have one N-pole and one S-pole. If the motor has four poles, it will have 2 N-poles and 2 S-poles and so on.
Synchronous speed in an electric motor is the speed that is produced by the traveling magnetic filed wave as it rotates around the stator magnetic circuit. The synchronous speed of a motor is equal to 120*f/p where f = the system frequency in Hz and p is equal to the number of poles in the motor.
All AC motors have two basic parts: (1) a stator winding and iron core and (2) a rotor winding and iron core that is free to rotate and is connected to the motor shaft. For a 3-phase induction motor, when the stator is energized by a three phase voltage source, a magnetic field will be produced that rotates at synchronous speed. As this magnetic flux cuts across the rotor winding it induces a current (via Faraday's law of induction) in the rotor winding which intern produces a second magnetic flux. These two magnetic fluxes both rotate at synchronous speed and couple together like two magnets and thus transfer torque directly to the rotor shaft.
Why induction motors have no pole slipping and why other motors have pole slipping. I will attempt to answer this but first let's define poles and synchronous speed in regards to electric motor operation.
Poles in an electric motor refer to the magnetic circuit poles and come in sets of two just like a common magnet. One is north (N) and one is south (S). If a motor has two poles, it will have one N-pole and one S-pole. If the motor has four poles, it will have 2 N-poles and 2 S-poles and so on.
Synchronous speed in an electric motor is the speed that is produced by the traveling magnetic filed wave as it rotates around the stator magnetic circuit. The synchronous speed of a motor is equal to 120*f/p where f = the system frequency in Hz and p is equal to the number of poles in the motor.
All AC motors have two basic parts: (1) a stator winding and iron core and (2) a rotor winding and iron core that is free to rotate and is connected to the motor shaft. For a 3-phase induction motor, when the stator is energized by a three phase voltage source, a magnetic field will be produced that rotates at synchronous speed. As this magnetic flux cuts across the rotor winding it induces a current (via Faraday's law of induction) in the rotor winding which intern produces a second magnetic flux. These two magnetic fluxes both rotate at synchronous speed and couple together like two magnets and thus transfer torque directly to the rotor shaft.
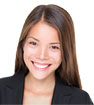


Category
Featured
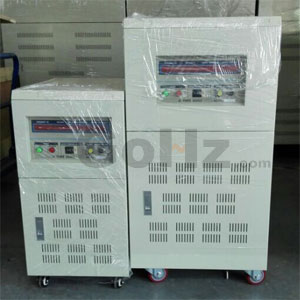
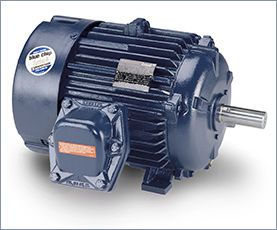
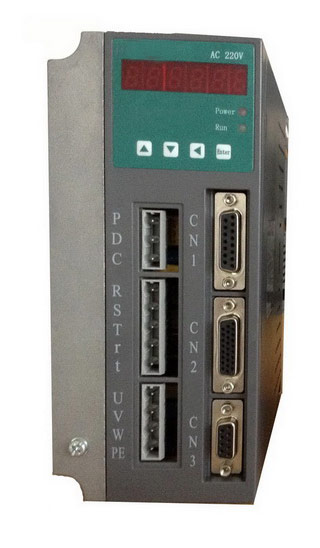