Motor
Q: I would like to know about any standard or documents or method, which will help to conduct accelerated life cycle test on electric motor. For example, if we are planning to give 10 years warranty on a motor, how long (short time) we should run the motor at rated condition to replicate the same impact. This is just an example.
A: First - you'd need to define the items that would be covered under such a warranty condition. Second - you'd need to decide what constitutes an acceptable failure rate during the warranty period.
For most manufacturers, this basically boils down to life cycle testing of a couple of key systems.
A: First - you'd need to define the items that would be covered under such a warranty condition. Second - you'd need to decide what constitutes an acceptable failure rate during the warranty period.
For most manufacturers, this basically boils down to life cycle testing of a couple of key systems.
I used a NEMA-design induction motor, which have fairly high inductance so they can be line-started. I don't recall the inductances, but I made sure to use a motor with a similar power rating to the variable frequency drive.
Don't worry about the inductance without the rotor. If you work through the equations you'll find that the stator R-L time constant dominates the current ripple at the switching frequency. Not enough flux crosses the air-gap at the switching frequency to make much difference.
The rotor does modify the inductance. You will have to be a little careful about how much voltage you apply to the phases, because you can easily generate too much current (a given, since there's no back-emf, either). But at the switching frequency, very little flux crosses the airgap so the rotor does not really figure into the equations for DC bus ripple current. And in this sort of testing, it's DC bus ripple that can accidentally destroy the variable frequency drive you are trying to verify!
Don't worry about the inductance without the rotor. If you work through the equations you'll find that the stator R-L time constant dominates the current ripple at the switching frequency. Not enough flux crosses the air-gap at the switching frequency to make much difference.
The rotor does modify the inductance. You will have to be a little careful about how much voltage you apply to the phases, because you can easily generate too much current (a given, since there's no back-emf, either). But at the switching frequency, very little flux crosses the airgap so the rotor does not really figure into the equations for DC bus ripple current. And in this sort of testing, it's DC bus ripple that can accidentally destroy the variable frequency drive you are trying to verify!
CO2 is probably the best alternative if an Oily winding has to be cleaned on site but is it not 100% and it is not straight forward. You should make your customer aware of all the facts. CO2 is a wonderful cleaning alternative. We have 6 CO2 machines and we use CO2 on a regular basis to clean windings and it is very effective in most cases. The one area where it is not very effective is with oil. It is very difficult to remove oil from a winding using CO2. It can be done but is a much slower process than other types of contamination because it does not fall in the way that most contaminant do. It will move along the surface but it will not fall off. You move it along to a gathering point where you can wipe it off. Imagine a patch of oil on the floor. You could use CO2 to clean that oil patch from the floor and that part of the floor will become clean, but the oil will be on another section of the floor. CO2 tends to move the oil around but never remove it 100%. And remember, if you can't point the nozzle at it, you will not remove it.
I have worked a great deal designing PM synchronous servo motors and their systems. Generally I work with precisions of 20 micron or less, this application is only about 800 micron of positioning accuracy. Following are some of the principles that I use to guide me through applications that might help you.
First- Accuracy is a function of the system not just the motor. The motor is merely a device for converting current into torque or force. Your system is comprised of the following: The Load, this is the mechanical portion of the system including the work and cutters; stiffer is always better when it comes to precision and if your load is too flexible the required precision could be impossible. The Controller/Amplifier this is where the servo loop is closed, system tuning parameters are set and the current is regulated to the motor windings, it is best to speak with a manufacture representative to ensure that you have to correct control for you application as this can be a complex subject. The Encoder or feed-back device, higher resolution is always better; I find I need a minimum of 10x resolution to my desired system accuracy. Finally the Motor, in positioning application I generally find lower inertia is better for accuracy, but in velocity control (which sounds more like what you need) I find higher inertia to be better for accuracy; this is because velocity control applications tend not to need high accelerations or rapid changes in speed, this means high inertia is your friend, it tends to smooth things out and help maintain a constant speed.
First- Accuracy is a function of the system not just the motor. The motor is merely a device for converting current into torque or force. Your system is comprised of the following: The Load, this is the mechanical portion of the system including the work and cutters; stiffer is always better when it comes to precision and if your load is too flexible the required precision could be impossible. The Controller/Amplifier this is where the servo loop is closed, system tuning parameters are set and the current is regulated to the motor windings, it is best to speak with a manufacture representative to ensure that you have to correct control for you application as this can be a complex subject. The Encoder or feed-back device, higher resolution is always better; I find I need a minimum of 10x resolution to my desired system accuracy. Finally the Motor, in positioning application I generally find lower inertia is better for accuracy, but in velocity control (which sounds more like what you need) I find higher inertia to be better for accuracy; this is because velocity control applications tend not to need high accelerations or rapid changes in speed, this means high inertia is your friend, it tends to smooth things out and help maintain a constant speed.
The troubleshooting guide outlines a comprehensive variety of motor problems. Generally the categories are arranged according to symptoms offering brief suggestions concerning what to look for when investigating motor failures (why motor fails?) and often providing advice on how to correct the problem once it has been identified.
Motor Shuts Off Before Full Speed
A. Motor also hums (single phase motor)
Run winding may have a loose connection - disassemble motor in order to make the appropriate repair
C. Excessively low voltage.
F. Bad capacitor Run winding is burned out - motor must be replaced or rewound
B. Overloaded
Reduce the load. A reasonable overload or voltage drop of 10-15% will reduce speed only 1 to2 percent.
A report of any greater drop would be questionable.
D. Inaccurate method of measuring RPM
Check meter using another device or method.
E. Wrong connections
Motor Shuts Off Before Full Speed
A. Motor also hums (single phase motor)
F. Bad capacitor
B. Overloaded
D. Inaccurate method of measuring RPM
E. Wrong connections
Starts If Shaft Is Spun
A. This will occur with a split phase or capacitor start motor only.
B. Check to see if the start winding is burned out.
A. This will occur with a split phase or capacitor start motor only.
B. Check to see if the start winding is burned out.
- If so, replace the winding or rewind motor completely.
- Disassemble motor in order to make the appropriate repairs.
- Disassemble motor in order to make the appropriate repair.
Heat is the ultimate threat to a motor's longevity. Excessive heat literally cooks the components of a motor, causing material breakdown, and ultimate failure. It is well known by most motor folks: For every 10 degrees centigrade increase in the operating temperature, there is a corresponding 50% loss in motor life.
It is important during the selection process, the installation, the ensuing operation and maintenance, to focus on eliminating, or at least reducing, all potential causes of overheating.
For example, every motor has nameplate information that defines its operating temperature range and its tolerance to temperature rise.
Adherence to voltage, phase and frequency tolerances insure that the "fuel"for the motor's operation will be as pure as possible.
Regularly scheduled preventive maintenance that focuses on the motor's physical and electrical environment can help detect potential overheating problems.
Ultimately, any operation's goal is to produce the most using the least,saving as much as possible. Well thought out strategies that keep motors working longer help to meet the economic goals.
It is important during the selection process, the installation, the ensuing operation and maintenance, to focus on eliminating, or at least reducing, all potential causes of overheating.
For example, every motor has nameplate information that defines its operating temperature range and its tolerance to temperature rise.
Adherence to voltage, phase and frequency tolerances insure that the "fuel"for the motor's operation will be as pure as possible.
Regularly scheduled preventive maintenance that focuses on the motor's physical and electrical environment can help detect potential overheating problems.
Ultimately, any operation's goal is to produce the most using the least,saving as much as possible. Well thought out strategies that keep motors working longer help to meet the economic goals.
Some motors are designed to operate at two, three, or four separate designated speeds. The speed of an induction motor depends on the number of poles built into the motor and the frequency of the electrical power supply. Multi-speed motors are available up to 500 hp, and are very reliable, but have several drawbacks.
The stator slots have to be bigger than those of single-speed motors in order to accommodate two or more sets of windings. As a result, the motors are bulkier and cannot be easily retrofitted. The current-carrying capacity of the copper is poorly utilized since only one set of windings is active at a time. Because of their dual speed design, however, they still have lower operating efficiencies than comparably sized single speed motors.
Multiple speed motor starters typically cost up to twice as much as single-speed motor starters. Multi-speed motors themselves cost 50-100 percent more than single-speed motors. Two-speed motors can be used to save energy in such applications as air volume control in facilities that have large differences in day-to-night or weekday-to-weekend air flow requirements. A dual speed fan rated for 1,200 and 1,800 rpm, for instance, can reduce fan energy requirements at night and on weekends by 70 percent.
The stator slots have to be bigger than those of single-speed motors in order to accommodate two or more sets of windings. As a result, the motors are bulkier and cannot be easily retrofitted. The current-carrying capacity of the copper is poorly utilized since only one set of windings is active at a time. Because of their dual speed design, however, they still have lower operating efficiencies than comparably sized single speed motors.
Multiple speed motor starters typically cost up to twice as much as single-speed motor starters. Multi-speed motors themselves cost 50-100 percent more than single-speed motors. Two-speed motors can be used to save energy in such applications as air volume control in facilities that have large differences in day-to-night or weekday-to-weekend air flow requirements. A dual speed fan rated for 1,200 and 1,800 rpm, for instance, can reduce fan energy requirements at night and on weekends by 70 percent.
Letters or numbers that are the same would normally go together. Your example is RR, YY, BB. They could be XX, YY, ZZ or 11, 22, 33. This is very often done on larger motors because two smaller cables are easier to handle than one large cable.
With the USA and Canada single speed motors: If you see a numbering system from1-6 it normally means that the motor is designed for a WYE-DELTA Start. If you see a numbering system from 1-9 this would indicate a dual voltage winding with the low voltage being 50% of the high voltage. This termed a 1WYE-2Wye connection or 1Delta-2 Delta. This would indicate a series connection for the high voltage and a parallel connection for the low voltage. The number of parallels can change but the low voltage will always have double the Parallels of the high voltage.
In Europe the main identification is lettering. U-V-W, X-Y-Z or U1, V1, W1 and U2, V2 W2 in the first example U and X are a phase, V and Y are a phase and W and Z are a phase. The phases are normally connected in series, (WYE), for the higher voltage, (possibly 380) and you can connect the phases in Parallel, (Delta) for a rated voltage of 58% of the higher voltage: (220-volts). This is also evident in the medium voltage motors that are rated 2300/4160. Wye Connected for 4160 and Delta connected for 2300. Don't you dare mix them up and connect for the wrong voltage.
With the USA and Canada single speed motors: If you see a numbering system from1-6 it normally means that the motor is designed for a WYE-DELTA Start. If you see a numbering system from 1-9 this would indicate a dual voltage winding with the low voltage being 50% of the high voltage. This termed a 1WYE-2Wye connection or 1Delta-2 Delta. This would indicate a series connection for the high voltage and a parallel connection for the low voltage. The number of parallels can change but the low voltage will always have double the Parallels of the high voltage.
In Europe the main identification is lettering. U-V-W, X-Y-Z or U1, V1, W1 and U2, V2 W2 in the first example U and X are a phase, V and Y are a phase and W and Z are a phase. The phases are normally connected in series, (WYE), for the higher voltage, (possibly 380) and you can connect the phases in Parallel, (Delta) for a rated voltage of 58% of the higher voltage: (220-volts). This is also evident in the medium voltage motors that are rated 2300/4160. Wye Connected for 4160 and Delta connected for 2300. Don't you dare mix them up and connect for the wrong voltage.
An induction motor operates at the frequency of the supply feeding it. One may vary the speed by varying the applied frequency.
To operate, the motor requires flux in the iron -- or more specifically in the gap between the rotor and stator. The rotor typically turns at a speed slightly lower than the rotational speed of the stator field (which depends on the frequency). This difference in speed is known as the slip, and is load-dependent (note: AC motors with permanent rotor magnets exhibit no-slip (synchronous) operation). The slip causes the flux to cut through the rotor windings, inducing a current to flow in the rotor. The frequency of the current flow is equal to the slip frequency and can never be zero.
The induction motor is designed as a compromise between iron loss and copper loss. If you reduce the turns on the stator, the copper loss would decrease due to lower resistance, but the flux in the iron would increase causing an increase in the iron loss. If the flux in the iron is too high, the losses increase dramatically and the iron is said to be saturated. The goal is to operate close to saturation to minimize the copper loss but not in saturation to minimize the iron loss. The rated voltage reflects the optimum flux at the rated frequency. As you reduce the frequency applied to the motor, you need to reduce the voltage in order to retain the same flux density. If you don't , the flux density will increase and the iron will saturate.
To operate, the motor requires flux in the iron -- or more specifically in the gap between the rotor and stator. The rotor typically turns at a speed slightly lower than the rotational speed of the stator field (which depends on the frequency). This difference in speed is known as the slip, and is load-dependent (note: AC motors with permanent rotor magnets exhibit no-slip (synchronous) operation). The slip causes the flux to cut through the rotor windings, inducing a current to flow in the rotor. The frequency of the current flow is equal to the slip frequency and can never be zero.
The induction motor is designed as a compromise between iron loss and copper loss. If you reduce the turns on the stator, the copper loss would decrease due to lower resistance, but the flux in the iron would increase causing an increase in the iron loss. If the flux in the iron is too high, the losses increase dramatically and the iron is said to be saturated. The goal is to operate close to saturation to minimize the copper loss but not in saturation to minimize the iron loss. The rated voltage reflects the optimum flux at the rated frequency. As you reduce the frequency applied to the motor, you need to reduce the voltage in order to retain the same flux density. If you don't , the flux density will increase and the iron will saturate.
Inverter duty and vector duty describe a class of AC induction motors that are specifically designed for use with frequency inverter. The high switching frequencies and fast voltage rise times of frequency inverters can produce high voltage peaks in the windings of standard AC motors that exceed their insulation break down voltage. Also, operating motors for an extended time at low motor rpm reduces the flow of cooling air, which results in an increase in temperature. NEMA-rated inverter- or vector-duty motors use high-temperature insulating materials that can withstand higher voltage spikes and operating temperatures. This reduces the stress on the insulation system.
Frequency inverter variable loads such as pumps, hydraulic systems, and fans. In these applications, motor efficiency is often poor due to operation at low loads and can be improved by using a frequency inverter in place of speed controllers such as belts and pulleys, throttle valves, fan dampers, and magnetic clutches. E.g., a pump or fan, controlled by a frequency inverter, running at half-speed consumes only one-eighth of the energy com pared to one running at full speed, resulting in consider able energy savings.
Frequency inverter variable loads such as pumps, hydraulic systems, and fans. In these applications, motor efficiency is often poor due to operation at low loads and can be improved by using a frequency inverter in place of speed controllers such as belts and pulleys, throttle valves, fan dampers, and magnetic clutches. E.g., a pump or fan, controlled by a frequency inverter, running at half-speed consumes only one-eighth of the energy com pared to one running at full speed, resulting in consider able energy savings.
Unlike other types of single-phase motors, shaded-pole motors have only one main winding and no start winding or switch. As in other induction motors, the rotating part is a squirrel-cage rotor. Starting is by means of a design that uses a continuous copper loop around a small portion of each motor pole. Currents in this copper loop delay the phase of magnetic flux in that part of the pole enough to provide a rotating field. This rotating field effect produces a very low starting torque compared to other classes of single-phase motors. Although direction of rotation is not normally reversible, some shaded-pole motors are wound with two main windings that reverse the direction of the field. Slip in the shaded-pole motor is not a problem, as the current in the stator is not controlled by a counter-voltage determined by rotor speed, as in other types of single-phase motors. Speed can therefore be controlled merely by varying voltage, or through a multitap winding.
Shaded-pole motors are best suited to low-power household application, because the motors have low starting torque and efficiency ratings. Because of the weak starting torque, shaded-pole motors are built only in small sizes ranging from 1/20 to 1/6 hp. Applications for this type of motor include fans, can openers, blowers, and electric razors.
Shaded-pole motors are best suited to low-power household application, because the motors have low starting torque and efficiency ratings. Because of the weak starting torque, shaded-pole motors are built only in small sizes ranging from 1/20 to 1/6 hp. Applications for this type of motor include fans, can openers, blowers, and electric razors.
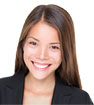


Category
Featured
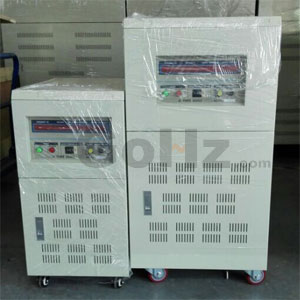
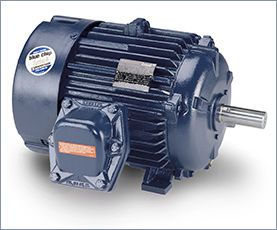
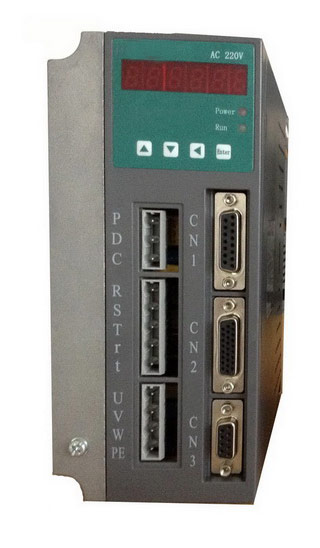