Motor control
In theory, it is possible to control the rotor flux vector in any n-phase machine. People play with five and six phase machines all the time but the single phase machine seems to be the singularity because of the bidirectional air gap flux. I think mathematically we can work out some way of controlling that flux but as others have said here, why bother?
One more assumption that I see is that the single phase machine is incapable of higher powers. The single phase machine can be designed to very high powers, but we don't do it because the machines would be much larger than a 3 phase machine and take up more material. In fact there are relatively large single phase machines in the integral power range, designed mainly for rural use, where three phase power is not available.
Capacitor start single phase motors have a stationary switch & centrifugal switch that switch the motor out of the start winding to the run winding. The centrifugal switch requires the rotor to turn at a certain speed (apprx. 3/4 speed) to engage the contacts on the stationary switch. Its possible the motor would never get out of the start winding and quickly fry.
One more assumption that I see is that the single phase machine is incapable of higher powers. The single phase machine can be designed to very high powers, but we don't do it because the machines would be much larger than a 3 phase machine and take up more material. In fact there are relatively large single phase machines in the integral power range, designed mainly for rural use, where three phase power is not available.
Capacitor start single phase motors have a stationary switch & centrifugal switch that switch the motor out of the start winding to the run winding. The centrifugal switch requires the rotor to turn at a certain speed (apprx. 3/4 speed) to engage the contacts on the stationary switch. Its possible the motor would never get out of the start winding and quickly fry.
I did some analysis on an induction motor some years ago re speed or torque control at low speed without a sensor. I concluded that there was nothing to sense and that it could not be done. In the last twenty years I have seen some improvement in sensorless control, but have not seen anyone do it at zero speed. I build motion bases using induction motors as servo motors, and I do get full torque at stall with a V/f drive using a feedback pot for position control.
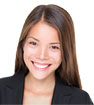


Category
Featured
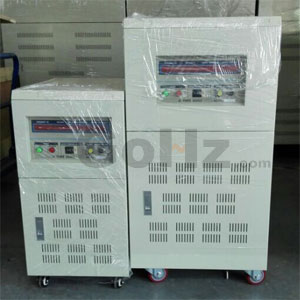
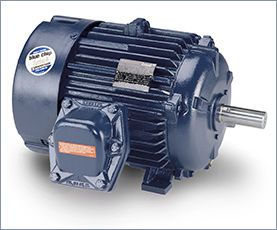
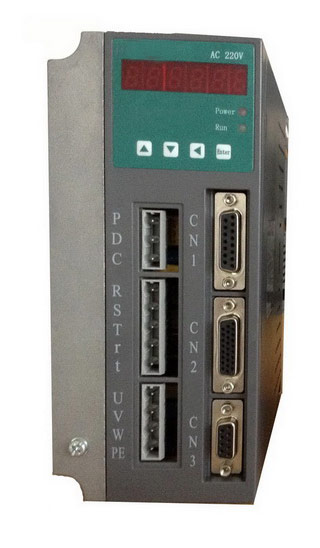