Motor repair
Motor Failed…Who Cares?
Too often we hear maintenance & reliability experts downplay the data analysis or testing of motors that have failed from a stator fault. "Why would you need test equipment to test a stator fault?" we might hear. The mistake these "experts" make is to assume that troubleshooting a motor begins with failure analysis. Smart motors are on the market, but we haven't seen any with a big red flag that pops up with the words "STATOR FAULT" when it trips or fails to start. The reality most non-clairvoyant technicians face is they don't know exactly what failed, or if anything failed at all. Is it the motor, the load, the starter or maybe a nuisance trip? Remember a very important role of your predictive technologies is to assist the technicians in a quick recovery effort of production in the unfortunate situation of an unplanned outage. Performing some quick tests such as phase resistance, phase inductance, and ground wall tests can allow the technician to isolate quickly focus on or off of the electric motor and hasten good decision-making in deciding if a repair or replacement is necessary. A simple phase imbalance test may just prevent you from replacing a motor that doesn't need to be replaced.
It's Not Always the Motor's Fault
When testing a motor it is good practice to thoroughly test the entire motor circuit. A Wound Rotor Motor has two circuits – the stator circuit, which is very similar to a standard AC induction motor, and a rotor circuit. The rotor circuit usually consists of rotor windings, rings and brushes, and a resistor bank controlled using contactors. Depending on the application, the rotor circuit is used to control the torque, speed, or startup current of the motor. The external portion of the rotor circuit usually consists of an external resistor bank with a number of resistance steps. An unbalance of resistance in the resistor bank will cause an unbalance of the flux in the rotor creating a situation similar to a broken rotor bar. There are several tests using the MCEMAX that can be performed to evaluate this situation. With the motor de-energized, a standard test can be performed on each step of the resistor bank circuit to ensure resistance is balanced through each step and when the resistor bank is fully shorted out. With the motor running, a rotor evaluation test can be performed to look for a current unbalance during startup and after the motor is at full speed. An In-Rush test can be used to evaluate startup and switching times when troubleshooting anomalies in the rotor circuit.
Too often we hear maintenance & reliability experts downplay the data analysis or testing of motors that have failed from a stator fault. "Why would you need test equipment to test a stator fault?" we might hear. The mistake these "experts" make is to assume that troubleshooting a motor begins with failure analysis. Smart motors are on the market, but we haven't seen any with a big red flag that pops up with the words "STATOR FAULT" when it trips or fails to start. The reality most non-clairvoyant technicians face is they don't know exactly what failed, or if anything failed at all. Is it the motor, the load, the starter or maybe a nuisance trip? Remember a very important role of your predictive technologies is to assist the technicians in a quick recovery effort of production in the unfortunate situation of an unplanned outage. Performing some quick tests such as phase resistance, phase inductance, and ground wall tests can allow the technician to isolate quickly focus on or off of the electric motor and hasten good decision-making in deciding if a repair or replacement is necessary. A simple phase imbalance test may just prevent you from replacing a motor that doesn't need to be replaced.
It's Not Always the Motor's Fault
When testing a motor it is good practice to thoroughly test the entire motor circuit. A Wound Rotor Motor has two circuits – the stator circuit, which is very similar to a standard AC induction motor, and a rotor circuit. The rotor circuit usually consists of rotor windings, rings and brushes, and a resistor bank controlled using contactors. Depending on the application, the rotor circuit is used to control the torque, speed, or startup current of the motor. The external portion of the rotor circuit usually consists of an external resistor bank with a number of resistance steps. An unbalance of resistance in the resistor bank will cause an unbalance of the flux in the rotor creating a situation similar to a broken rotor bar. There are several tests using the MCEMAX that can be performed to evaluate this situation. With the motor de-energized, a standard test can be performed on each step of the resistor bank circuit to ensure resistance is balanced through each step and when the resistor bank is fully shorted out. With the motor running, a rotor evaluation test can be performed to look for a current unbalance during startup and after the motor is at full speed. An In-Rush test can be used to evaluate startup and switching times when troubleshooting anomalies in the rotor circuit.
There are some customers out there that have their larger motors repaired at one facility and their smaller motors repaired at others. There are also customers who expect you to take care of all their motor repairs no matter how small or how large.
It has become increasingly difficult to make a profit by repairing smaller motors, so when they are standard / off the shelf motors there is a small profit to be made by replacing the motor as opposed to a loss when the motor is repaired. In the case of smaller Specialty or OEM motors the repair price is most often more expensive than new but sometimes the new motor has an extended delivery. In cases like this when delivery is a factor we give a fixed price prior to repair. In 99% of these cases the customer will tell us to proceed. The internet has made it much easier to source the OEM Motor and obtain a price and delivery quite quickly.
Where we will subcontract a repair to another facility is on the rewind of small armatures. Most of the larger facilities do not have the equipment required to economically rewind a small armature but there are some shops that specialize in that aspect of motor repair. we rarely encounter any problems when we subcontract this type of work. We do al the dismantling and assembly work that is required and we get a price ahead of time from the subcontractor. the customer gets the total price ahead of time and issues a purchase order or gives a verbal go ahead. The only time we run into problems is when the subcontractor does not meet the delivery date.
It has become increasingly difficult to make a profit by repairing smaller motors, so when they are standard / off the shelf motors there is a small profit to be made by replacing the motor as opposed to a loss when the motor is repaired. In the case of smaller Specialty or OEM motors the repair price is most often more expensive than new but sometimes the new motor has an extended delivery. In cases like this when delivery is a factor we give a fixed price prior to repair. In 99% of these cases the customer will tell us to proceed. The internet has made it much easier to source the OEM Motor and obtain a price and delivery quite quickly.
Where we will subcontract a repair to another facility is on the rewind of small armatures. Most of the larger facilities do not have the equipment required to economically rewind a small armature but there are some shops that specialize in that aspect of motor repair. we rarely encounter any problems when we subcontract this type of work. We do al the dismantling and assembly work that is required and we get a price ahead of time from the subcontractor. the customer gets the total price ahead of time and issues a purchase order or gives a verbal go ahead. The only time we run into problems is when the subcontractor does not meet the delivery date.
Individual organizations should consider developing their own customized Motor Management plan and policy. Some of the factors to consider are: extent of the repair - is it bearings or rewind, lead time for repair vs replace (special builds vs off the shelf), cost of new vs repair, single phase vs three phase, size (HP) of the product, efficiency of the failed motor vs efficiency of the replacement motor, warranty of the new vs repaired. Each organization's criteria and situation will factor into their individual decision tree.
Before you establish what %HP of the new motor value you will spend on repair, you need to know your repair facility. Derek is correct when he says that your service center needs to be following the "EASA AR-100 Recommended Practices". Following these repair guidelines, you will not lose efficiency in the repair process, in fact on larger HP's, there maybe opportunities to gain efficiency if your EASA shop gets EASA engineering involved. Additionally, the repair center should have a recognized and accredited Quality Assurance Program, such as ISO 9000. Weighing in on your decision, compare the new motor to what you are going to get back. Typically a new Nema T frame motor will be insulation Class F (155' C), many EASA facilities will rewind with insulation Class H (180' C) and you will immediately have a 25' C advantage over new. Also, a qualified individual rewinding at an EASA repair facility is (highly) likely to produce greater quality than the factory cranking out "production". Balance standards are also typically better which will yield longer bearing life when the motor is back in service.
Before you establish what %HP of the new motor value you will spend on repair, you need to know your repair facility. Derek is correct when he says that your service center needs to be following the "EASA AR-100 Recommended Practices". Following these repair guidelines, you will not lose efficiency in the repair process, in fact on larger HP's, there maybe opportunities to gain efficiency if your EASA shop gets EASA engineering involved. Additionally, the repair center should have a recognized and accredited Quality Assurance Program, such as ISO 9000. Weighing in on your decision, compare the new motor to what you are going to get back. Typically a new Nema T frame motor will be insulation Class F (155' C), many EASA facilities will rewind with insulation Class H (180' C) and you will immediately have a 25' C advantage over new. Also, a qualified individual rewinding at an EASA repair facility is (highly) likely to produce greater quality than the factory cranking out "production". Balance standards are also typically better which will yield longer bearing life when the motor is back in service.
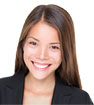


Category
Featured
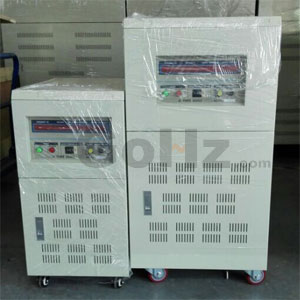
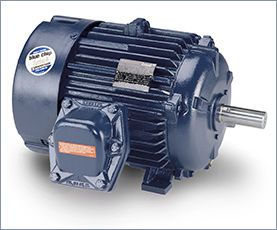
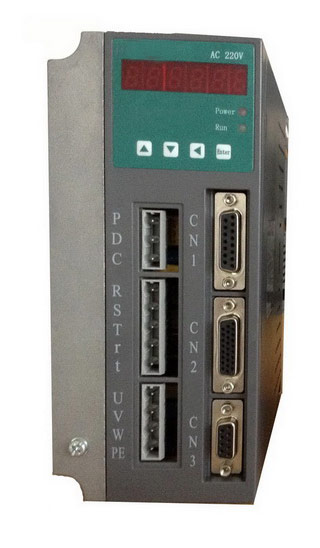